Understanding Industrial Electronic Equipment: A Comprehensive Guide
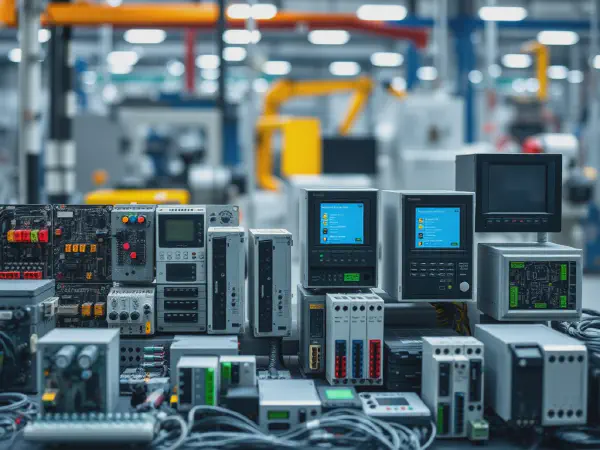
Understanding Industrial Electronic Equipment: A Comprehensive Overview
Industrial Electronic Equipment is essential in modern manufacturing and production processes, facilitating automation and enhancing operational efficiency. From programmable logic controllers to sensors and actuators, this equipment supports various industrial applications, ensuring seamless operations across diverse sectors.
The role of Industrial Electronic Equipment extends beyond simple automation; it plays a crucial part in energy management systems, telecommunications, robotics, and process control. These components are vital for enhancing productivity, optimizing energy consumption, and ensuring the safety of operations in industrial environments.
For superior performance in demanding environments, consider the innovative features of the rk220-01.
In an era of rapid technological advancements, industrial electronic equipment is continuously evolving. The incorporation of smart technologies such as the Internet of Things (IoT) and artificial intelligence (AI) is transforming the landscape, allowing for better data analysis, predictive maintenance, and overall system optimization.
When looking for durability and functionality, a water resistant keyboard is an essential addition to any workstation.
Safety is paramount in industries utilizing electronic equipment. Understanding the standards and compliance measures, risk assessment, emergency shutdown systems, and electrical safety practices is fundamental to maintaining a safe working environment for operators and equipment alike.
Furthermore, implementing regular maintenance and troubleshooting measures is critical for the longevity and reliability of Industrial Electronic Equipment. This article explores various types of equipment, their applications, safety considerations, emerging technologies, and maintenance best practices in industrial settings.
Applications of Industrial Electronic Equipment
One of the primary applications of Industrial Electronic Equipment is in automation in manufacturing and production. This includes the use of programmable logic controllers (PLCs) to automate assembly lines, material handling, and other repetitive tasks, resulting in higher efficiency and productivity.
Energy management systems are another significant application, enabling industries to monitor and control energy usage efficiently. By integrating smart meters and sensors, companies can analyze energy consumption patterns and optimize their usage, which leads to cost savings and reduced environmental impact.
Refer to the rk220-01 manual for detailed setup instructions and troubleshooting tips to optimize your device's performance.
Telecommunications equipment also falls under the umbrella of Industrial Electronic Equipment, facilitating communication between devices and systems in manufacturing setups. This includes modems, routers, and communication interfaces that ensure reliable data transfer and connectivity.
Control systems for robotics have revolutionized the manufacturing landscape, allowing for sophisticated automation solutions. By integrating sensors and actuators with controllers, industries can deploy robots for assembly, packaging, welding, and material handling tasks, thereby increasing precision and efficiency.
In the chemical industries, process control systems are crucial for monitoring and managing chemical reactions and processes. These systems use sensors to track variables such as temperature, pressure, and flow rate, ensuring that processes operate within designated parameters for safety and quality.
Types of Industrial Electronic Equipment
Programmable Logic Controllers (PLCs) are widely used in industrial automation for controlling machinery and processes. Their ability to be programmed for various tasks makes them versatile and essential components of modern manufacturing.
Sensors and actuators are critical in monitoring and controlling physical processes. Sensors gather data about environmental and operational conditions, while actuators convert this data into actionable outputs such as movements or adjustments in machinery.
Industrial PCs and Human-Machine Interfaces (HMIs) provide user-friendly platforms for operators to interact with industrial systems. They display real-time data and allow users to monitor and control processes effectively, improving overall operational efficiency.
Power supplies and converters are vital for ensuring that industrial electronic equipment receives a stable and consistent power supply. These devices convert and regulate electrical power to meet the specific needs of different equipment and systems.
Motor drives and control systems are essential for managing motor speed, torque, and direction in various applications, including conveyor systems, pumps, and fans. By precisely controlling motor functions, these systems enhance energy efficiency and performance.
Safety in Industrial Electronic Equipment
Understanding safety standards and compliance is crucial when working with Industrial Electronic Equipment. Regulations such as ISO 9001, IEC 61508, and OSHA guidelines ensure that equipment and processes meet safety requirements to protect workers and reduce risks of accidents.
Risk assessment techniques should be implemented to identify potential hazards associated with the use of industrial electronic equipment. Conducting thorough risk assessments helps in developing strategies to mitigate identified risks, ensuring a safer working environment.
Emergency shutdown systems are critical for averting catastrophic failures and accidents in industrial settings. These systems allow operators to quickly halt processes in the event of an emergency, minimizing risks to personnel and equipment.
Electrical safety practices include proper grounding, lockout/tagout procedures, and routine inspections of electrical systems. Adhering to these practices is vital in preventing electrical hazards and ensuring safe operations.
Protective device integration involves incorporating safety devices such as circuit breakers, fuses, and surge protectors into industrial systems. These devices play a significant role in safeguarding equipment and personnel against electrical faults and overloads.
Emerging Technologies in Industrial Electronic Equipment
The Internet of Things (IoT) is increasingly being integrated into industrial electronic equipment, enabling real-time data collection and analysis. This technology facilitates improved monitoring, control, and decision-making processes within industrial environments.
AI and machine learning applications are revolutionizing how industries operate. These technologies can analyze vast amounts of data generated by industrial electronic equipment, leading to improved efficiency, predictive insights, and enhanced decision-making capabilities.
Predictive maintenance technologies utilize data analytics and machine learning to forecast equipment failures before they occur. This proactive approach reduces downtime and maintenance costs by addressing issues before they escalate into significant problems.
Advancements in robotics have led to more sophisticated and versatile machines capable of performing an array of tasks in various industries. These robots can adapt to different operational needs, improving efficiency and productivity.
Trends in smart factory solutions are on the rise, with industries adopting interconnected systems and devices to streamline processes. Smart factories leverage advanced technologies for data-driven decision-making and enhanced operational effectiveness.
Maintenance and Troubleshooting of Industrial Electronic Equipment
Preventive maintenance involves scheduled inspections and routine upkeep of industrial electronic equipment to prevent breakdowns. Predictive maintenance, on the other hand, relies on data analytics to assess equipment condition and predict failures, allowing for more targeted maintenance efforts.
Identifying common faults and error codes is crucial for troubleshooting industrial electronic equipment. Operators should be familiar with these faults to respond quickly and effectively when issues arise, minimizing downtime and disruption.
Diagnostic tools and techniques, including oscilloscopes, multimeters, and software diagnostics, play a vital role in troubleshooting equipment. These tools help technicians identify and resolve issues efficiently, ensuring reliable operations.
Calibration and testing procedures are essential for ensuring that industrial electronic equipment operates within specified parameters. Regular calibration helps maintain accuracy and reliability, which is critical for effective operations.
Documentation and record-keeping of maintenance activities, troubleshooting incidents, and equipment configurations are vital for regulatory compliance and operational efficiency. Comprehensive records enable better decision-making and continuous improvement in maintenance practices.